A Comprehensive Overview to the Sorts Of Ceramic Finish on the Market
Ceramic finishes have become a pivotal option across different industries because of their special buildings and applications. From silica-based formulations recognized for their robustness to hybrid alternatives that merge numerous advantages, the choices available can be frustrating. Understanding the subtleties of each kind, including their specific advantages and ideal usage situations, is crucial for making notified choices. As we discover the distinct characteristics and applications of these coverings, the implications for performance and long life become significantly obvious, increasing concerns regarding which kind could finest match your demands.
Recognizing Ceramic Coatings
Ceramic coatings are advanced safety remedies that have obtained appeal in various industries, particularly in vehicle and aerospace applications. These coverings include a fluid polymer that, when cured, develops a resilient, hydrophobic layer on the surface area of the substrate. This layer offers improved resistance to environmental pollutants, UV radiation, and chemical direct exposure, therefore prolonging the life and visual appeal of the underlying product.
The fundamental element of ceramic coatings is silica, which adds to their firmness and resilience. The application procedure generally involves surface area preparation, application of the finish, and healing, which can be achieved via warm or UV light. When healed, ceramic coverings show phenomenal bonding buildings, allowing them to adhere highly to a range of surfaces, including metals, plastics, and glass.
In addition to their protective functions, ceramic finishings also offer simplicity of maintenance. Their hydrophobic nature lowers the adherence of dust and gunk, making cleaning simpler and less constant. In general, the adoption of ceramic finishings represents a significant improvement in surface protection modern technology, providing both useful and visual benefits across several fields.
Sorts Of Ceramic Coatings
Numerous types of ceramic coatings are available, each developed to meet certain efficiency requirements and applications - Auto Detailing. The most usual kinds consist of:
Silica-based Coatings: These coverings mainly contain silicon dioxide and are known for their toughness and chemical resistance. They are commonly used in auto and commercial applications.
Titanium Dioxide Coatings: Distinguished for their photocatalytic residential or commercial properties, titanium dioxide finishings are often applied in environments where self-cleaning and antifungal properties are preferable, such as in structure materials and automotive surfaces.
Zirconia Coatings: Identified by their high-temperature stability and thermal resistance, zirconia coatings are utilized in applications such as turbine engines and high-performance auto parts.
Alumina Coatings: Displaying superb solidity and thermal security, alumina finishings are often made use of in wear-resistant applications, consisting of cutting tools and industrial equipment. - scratch repair sarasota
Hybrid Coatings: Incorporating the buildings of various materials, crossbreed coatings use enhanced performance features, making them appropriate for one-of-a-kind and requiring applications.
Each sort of ceramic finish serves distinctive objectives, allowing customers to choose one of the most ideal option based on details ecological conditions and efficiency demands.
Benefits of Ceramic Coatings
Ceramic coverings, in specific, offer numerous benefits that make them increasingly prominent among makers and link customers alike. These coverings are resistant to scratches, chemicals, and UV rays, ensuring that the underlying surface continues to be protected over time.
Along with durability, ceramic coverings give excellent hydrophobic homes, permitting very easy cleansing and maintenance. This water-repellent nature lessens the adherence of dirt, grime, and various other pollutants, which can prolong the visual charm and functionality of the surface area. Ceramic layers can substantially improve thermal resistance, making them suitable for applications that sustain high temperature levels.
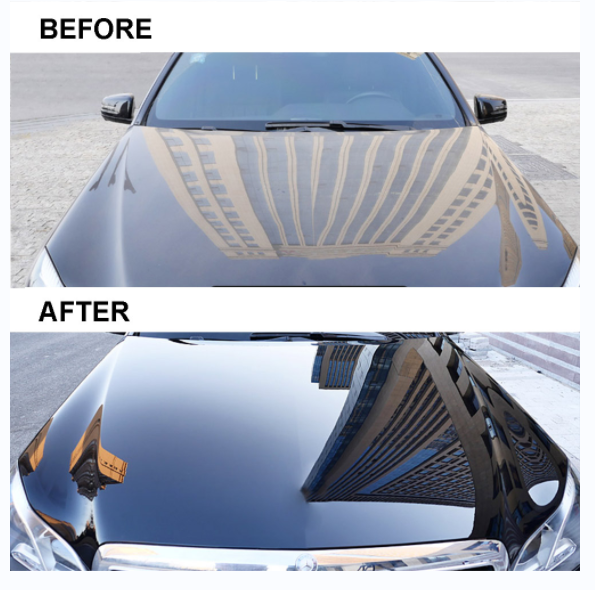
Application Refine
When applying ceramic layers, a precise approach is crucial to achieve ideal outcomes. A tidy surface area guarantees correct adhesion of the finish.
As soon as the surface is prepped, the next action is to use the ceramic finish. The layer needs to be applied in thin layers, as thicker applications can lead to unequal surfaces.
After application, the finishing needs a certain curing time, generally ranging from a couple of hours to a full day, depending on the product. Following these actions faithfully will visit this website make best use of the effectiveness and longevity of the ceramic coating, providing a sturdy protective layer for the surface area.
Maintenance and Long Life
To make sure the long life and effectiveness of a ceramic layer, normal upkeep is vital. Ceramic layers, recognized for their resilience and protective top qualities, call for particular care regimens to maximize their life-span and performance.
Along with routine cleaning, routine examinations are vital. Try to find indications of wear or damages, such as hydrophobic homes diminishing or surface flaws. If necessary, a light polish might be related to rejuvenate the finishing without stripping it away.
In addition, the application of a booster spray can enhance the coating's hydrophobic results and recover its gloss. This is specifically advantageous for layers that have remained in usage for a prolonged period. Eventually, by adhering to these upkeep techniques, one can dramatically the original source expand the life of a ceramic coating, guaranteeing that it proceeds to supply optimal protection against ecological factors and preserve the aesthetic appeal of the automobile.
Final thought
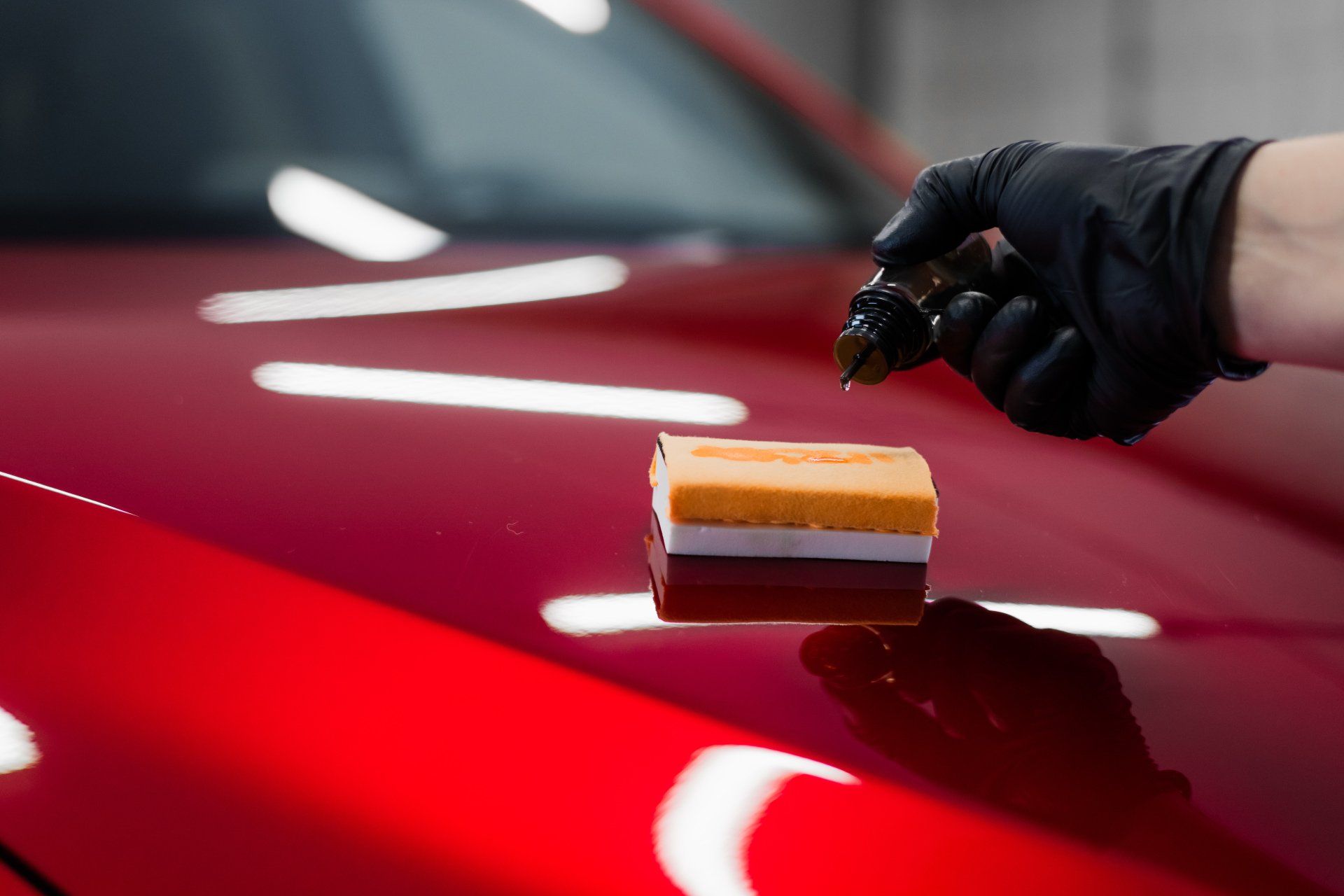